So sieht also ein "Hidden Champion" aus – ein erfolgreiches Unternehmen, das fast niemand auf dem Schirm hat. Am westlichen Stadtrand von Kempten, flankiert von Wald, Wiesen und einem kleinen Gewerbegebiet, liegt die Adam Hönig AG. Von außen ein niedriger Hallenkomplex, aus dem ein paar kleinwüchsige Schornsteine nach oben ragen.
Die Adam Hönig AG bringt Eisen für die unterschiedlichsten Kunden in Form
Doch hinter dem Werkstor, abgeschirmt von dicken Mauern und feuerfesten Türen, beginnt "die Hölle". So nennt Vorstand Roland Hübner schmunzelnd die Innereien der Kemptener Eisengießerei. Dort, wo dem Besucher Rauch und Hitze den Atem nehmen, wo Funken meterweit sprühen und rot glühendes Eisen in fast mannshohen Metallformen verschwindet. Eine Szene, wie sie früher im Ruhrpott weit verbreitet war, und das mitten im Allgäu.
Ein knappes Dutzend Eisengießereien gab es einst im Allgäu, vom Industriezulieferer bis zum Glockengießer. Die Adam Hönig AG ist als einziger Vertreter dieser schrumpfenden Zunft übrig geblieben. Das Überlebensrezept ist simpel: "Wir sind ein Tausendfüßler, kein Einbeiner", sagt Hübner. "Hätten wir uns auf eine Nische spezialisiert, gäbe es vermutlich auch uns nicht mehr."
So aber bringt die kleine Aktiengesellschaft Eisen für die unterschiedlichsten Kunden in Form und muss auch den aktuellen Umbruch in der Automobilindustrie nicht übermäßig fürchten. Die Lokomotivenbauer und Zulieferer Alstom, MTU und Henschel gehören zu den Abnehmern aus halb Europa, aber auch Maschinenbaufirmen wie Liebherr, MAN, Dornier, Grob, Bihler und Deckel Maho. Gehäuse für Erdölpumpen werden in Kempten ebenso gefertigt wie Planetenträger für Windräder, Seiltrommeln für Schiffe und Kräne oder Kupplungsgehäuse für Autos und Lastwagen. Die Größe der Gussstücke reicht vom ellenlangen Leitungsschieber bis zum 8,5 Tonnen schweren Maschinenbett.
Es begann mit der Herstellung von Herdplattem, Ofenrosten und Kochtöpfen
Bis zu 12.000 Tonnen Guss produziert das Unternehmen pro Jahr, der Umsatz betrug im Vorjahr 27 Millionen Euro, die Eigenkapitalquote liegt bei 60 Prozent. "Wir stehen gesund da", freut sich der energiegeladene Vorstand, der mit Begeisterung durch den Betrieb führt. Der 62-jährige Industriekaufmann, Bilanzbuchhalter und Controller ist in über 40 Jahren mit dem Gießereigeschäft groß geworden. Dabei hatte die Kemptener Eisengießerei nach dem Zweiten Weltkrieg auf kleiner Flamme begonnen.
Adam Hönig AG: Seit der Gründung in Familienbesitz
Die Kemptener Eisengießerei ist seit ihrer Gründung 1946 in Familienbesitz, wandelte aber immer wieder ihre Firmenstruktur.
Das Unternehmen begann als OHG, wurde 1972 zu einer Familiengesellschaft (KG) und 1980 zur GmbH & Co. 2001 folgte die Umwandlung der Gießerei in eine Aktiengesellschaft.
Die Anteile werden von Nachfahren des Gründers Adam Hönig gehalten. Den Aufsichtsrat bilden Wolfgang Pfefferle, Heidi Ernst und Oliver Mekiska.
Die Umwandlung zur AG hatte vor allem den Zweck, das Gussvolumen zu steigern und nötige Investitionen zu stemmen. Seit 2005 wurden insgesamt 30 Millionen Euro für neue Guss- und Verarbeitungstechnik, aber auch für den Umweltschutz ausgegeben.
Zu Letzterem gehört der Einbau von Entstaubungsanlagen, einer Wärmerückgewinnung sowie Abluftfiltern mit Überwachungssensoren. Drei Millionen Euro sollen noch in neue Be- und Entlüftungen und die Optimierung der Arbeitsplätze fließen.
Die AG zählt unter den Handformern zu den führenden der 300 Eisengießereien in Deutschland. Täglich werden in Kempten 60 bis 70 Tonnen Flüssigeisen verarbeitet. (raf)
Adam Hönig, der aus Siebenbürgen stammte, gründete das Unternehmen 1946 in einer angemieteten Halle nahe der Innenstadt. Den ersten Kupolofen hatte er aus Rohrabfällen zusammengeschweißt.
Die Herstellung von Herdplatten, Ofenrosten und Kochtöpfen sorgte für einen raschen Aufschwung, sodass die Produktion bald in ein neues Gebäude am heutigen Standort verlagert wurde. Per Bahn wurde die Gießerei dort bis 1991 mit Roheisen, Sand und Koks für die Öfen versorgt. "Damals hat Firmenchef Adam Hönig den fertigen Guss auch mal mit Moped und Anhänger bis nach Halblech ausgeliefert", erzählt Hübner. "In dieser Zeit wurde vieles per Handschlag geregelt, bezahlt wurde oft nach Kassenlage." 1960 zählte die spätere Aktiengesellschaft bereits 80 Mitarbeiter, 2004 waren es fast 200 – eine Zahl, die nach der Bankenkrise 2009/2010 auf 170 schrumpfte und seitdem stabil ist.
Die Öfen verbrauchen 14 bis 15 Millionen Kilowattstunden Strom im Jahr
Lange Jahre waren bei der Adam Hönig AG schwerfällige Kaltwindkupolöfen im Einsatz, die alles andere als umweltfreundlich waren und die Bewohner umgebender Häuser belasteten. "Der Kohlendioxid-Ausstoß war hoch", erinnert sich Hübner. "Und wenn wir vor dem Guss den Ofendeckel geöffnet haben, war die Wäsche auf den Balkonen der Nachbarschaft schwarz."
Seit 2007 wird das Roheisen, das in der Regel aus Deutschland und Brasilien stammt, nur noch in Elektroöfen erhitzt. Um Ressourcen zu schonen und Kosten zu senken (die Tonne Roheisen schlägt aktuell mit 380 bis 450 Euro zu Buche), werden dem Rohstoff ausrangierte Bahnschienen, Stanzabfälle und Gussreste aus dem eigenen Firmenkreislauf beigemengt. Die vier Schmelztiegel mit einem Fassungsvermögen von insgesamt 18 Tonnen bringen das Metall binnen einer Stunde auf 1350 bis 1450 Grad. "Die Öfen sind sehr effektiv, fressen aber 14 bis 15 Millionen Kilowattstunden Strom im Jahr", sagt Hübner. Wirtschaftlich produzieren könne sein Unternehmen da nur, weil es teilweise von der Ökostrom-Umlage befreit ist und ein zertifiziertes Energie-Management eingeführt hat.
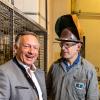
Mehrere Tagen vergehen, bis ein Gussstück abkühlt
"Am Grundprinzip des Eisengusses hat sich seit 5000 Jahren nichts geändert", erläutert der Vorstand. Der Unterschied liegt in den Details: Heute kommen je nach Gussstück und Kundenwunsch etwa 30 verschiedene Rezepturen zum Einsatz. "Das ist wie in der heimischen Küche", flachst der Vorstand. So "würzen" die Eisenkocher ihr Gebräu mit Kupfer, Nickel und synthetischen Zusätzen, um Eigenschaften wie Zugfestigkeit oder Härte zu beeinflussen. Aber auch teure Exoten wie Vanadium werden verwendet, das 40 Euro pro Kilo kostet und den Guss noch härter und verschleißbeständiger machen soll.
Doch bevor das rot glühende Metall den Schmelzofen und danach die von schweren Hebekränen gehaltenen Transportpfannen verlassen darf, müssen erst die Modellbauer ihren Part abliefern. Sie fertigen von Hand oder am Automaten Gussformen aus Holz oder Kunststoff. Sie sind Vorlagen für die Hohlform, die später vom flüssigen Metall geflutet wird. "Diese Vorarbeit ist der Garant für einen guten Guss", betont Hübner. Als Vorlage dienen 3D-Zeichnungen des Kunden.
Damit Formkern und Außenform nicht verrutschen, werden beide in einem massiven Formkasten platziert. Zur Fixierung dient Quarzsand, der sämtliche Zwischenräume ausfüllt und mit Milchsäure und Furanharz getränkt wird. "Das wird in wenigen Minuten hart wie Beton", sagt der Gießerei-Chef. Etwa 200 Tonnen Sand kommen pro Tag zum Einsatz, wobei sich dieser Rohstoff mehrfach recyceln lässt.
Es dauert mehrere Tage, bis ein Gussstück von etlichen Tonnen abgekühlt ist. Dann zeigt sich, ob das Team gut gearbeitet hat. "Lufteinschlüsse, Hohlräume und Schlackereste sind tabu", erläutert Vertriebsleiter Manfred Szymanski. Damit keine Sollbruchstellen entstehen, darf der Gießvorgang nie unterbrochen werden. Bei großen Stücken wird das glühende Eisen deshalb von zwei Seiten eingefüllt. Auch bei den Maßen der Endprodukte geht es exakt zu: Gerade mal einen Millimeter beträgt die erlaubte Toleranz im Schnitt – den einprozentigen Materialschwund beim Aushärten bereits eingerechnet.
Roland Hübner: "Tradition und Moderne passen in der Schwerindustrie gut zusammen"
Die Arbeit in den teils 60 Jahre alten Hallen ist ungeachtet moderner Hilfsmittel und der mit Millionenaufwand installierten Ablufttechnik ein Knochenjob. Das gilt nicht nur für die Männer an Öfen und Pfannen, sondern auch für die späteren Arbeitsschritte – etwa das Glätten, Entgraten und Grundieren der Gussstücke. Dennoch tendiere die Fluktuation "gegen Null", sagt Hübner. "Wir sind wie eine große Familie. Ich kenne sogar den Geburtstag von jedem einzelnen."
Das gelte auch für die acht Azubis, die die Adam Hönig AG in Fertigung, Modellbau und Büro beschäftigt. Ob jemand für diese Branche taugt, zeigt sich laut Vorstand übrigens sofort: "Entweder er bleibt bei uns oder er ist schon nach zwei Stunden wieder weg."
Vor zwei Jahren hat die Gießerei mit Unterstützung der Hochschule Kempten ein neues Daten-Managementsystem auf Basis einer App entwickelt. Seitdem wird jeder einzelne Arbeitsschritt mittels QR-Code gespeichert und ausgewertet. Das passt zu Hübners Credo: "Tradition und Moderne passen auch in der Schwerindustrie gut zusammen."
Das könnte Sie auch interessieren:
- Aichacher Firma Juzo: Medizinische Strümpfe dürfen auch bunt sein
- Wie die Firma DTB aus Rennertshofen den Generationenwechsel stemmt
- Bio-Hanf-Biermix und Bambus-Pflaster: Das gibt's auf der Biofach
- Burj Khalifa, Lakhta Tower & Co.: Firma aus der Region baut weltweit an Wolkenkratzern
Wir möchten wissen, was Sie denken: Die Augsburger Allgemeine arbeitet daher mit dem Meinungsforschungsinstitut Civey zusammen. Was es mit den repräsentativen Umfragen auf sich hat und warum Sie sich registrieren sollten, lesen Sie hier.