Wie wäre es jetzt noch mit rabiaten Hammer- und Amboss-Klängen aus Wagners Ring der Nibelungen oder gleich mit brachialer Rockmusik von Rammstein? Schließlich sprühen die Funken gelb und rot. Es knistert. Hitzewellen schieben sich durch die Industriehalle in Augsburg. Heavy Metal, aber ohne Musik. Männer im silbernen Strahlenschutzanzug verrichten mit ruhiger Hand die Arbeit. Ihre Köpfe stecken in ebenso silberfarbenen Schutzhelmen. Es riecht nach Eisen, verbranntem Harz, eben Industrie, harter Arbeit.
Nur Männer sind zu sehen. Ganz ruhig und sanft gehen sie miteinander um. Keiner schreit in der Stunde der Geburt eines neuen, riesigen Motors, der einmal ein Kraftwerk in der Türkei zum Leben erwecken soll. Die Männer kennen sich lange. Morgens vor sechs Uhr spielt jeder sein Instrument in der Augsburger Sinfonie aus noch 1400 Grad heißem Eisen, das in eine Form aus Sand und Harz gegossen werden soll.
110 Tonnen flüssiges Eisen fließen bei 1350 Grad
Vier Töpfe mit der bedrohlichen Fracht werden sich über kräftige Krane zum Ort ihrer Bestimmung bewegen. Die Männer nennen sie Pfannen. Aus ihnen ergießen sich 110 Tonnen flüssiges Eisen. Bei genau 1350 Grad soll es in zwei Becken fließen und über Röhren in den Hohlkörper der zuvor aufwendig aus Quarzsand und Harz gebauten Motorblock-Form vordringen. Noch sind es 1386 Grad. Die Männer müssen warten. Sie sind ruhig.
Immer wieder haben die Arbeiter zuvor von den Pfannen oben die Schlacke mit langen Schabern abgekratzt, sodass Funken sprühen. Schon am Vorabend begann die große Eisenschmelzerei, die Unmengen elektrischer Energie verbraucht. Die Hülle des Motors stammt zu 100 Prozent aus recyceltem Material. In Augsburg wird Schrott zu neuen Motoren, ob für Kreuzfahrtschiffe, schwimmende Kräne, schnelle Fähren, Transportboote für die Öl- und Gasindustrie, aber auch für Kraftwerke. Die Gießerei ist etwas Besonderes. Außerhalb des Ruhrgebiets können in Deutschland nur in Augsburg derart große Bauteile gegossen werden. Die hafenlose Stadt am Lech spielt in der maritimen Welt eine wichtige Rolle. Die dort sitzende und zu VW gehörende Firma MAN Diesel & Turbo sieht sich als weltweit führender Anbieter großer Schiffs- und Kraftwerksmotoren. Verständnisvoll nehmen viele Augsburger die Verkehrseinschränkungen hin, wenn die Motoren-Ungetüme „ihrer
Der MAN-Diesel- und Turbo-Chef ist auch sehr früh aufgestanden, um wieder einmal das Schauspiel der Geburt eines Motors zu erleben. Uwe Lauber trägt neben Sicherheitsschuhen und Spezialbrille eine Jeanshose und eine ältere Jacke, das geeignete Outfit für eine Gießerei, deren Gerüche die Kleidung rasch annimmt. Nur einige Politiker, die an dem Morgen auch zu den Gästen der Augsburger Funken-Musik gehören, verzichten nicht auf Anzug und Krawatte.
Jeder Motor ein Unikat
Lauber jedenfalls scheint es in der Gießerei besonders zu gefallen. Frühmorgens schwärmt er: „Das ist wunderbar hier, eben richtiges Handwerk in Zeiten der Digitalisierung.“ Jeder Motor sei ein Unikat. Der Diesel-Chef sagt: „Hier kommt es vor allem auf die Menschen an.“
Vitus Fischer ist einer, auf den es besonders ankommt. Schon 40 Jahre arbeitet der 55-Jährige für MAN in Augsburg. Er ist einer der Männer im silbernen Schutzanzug. Fischer kratzt Schlacke von der Pfanne ab, geht einige Schritte zurück, nimmt seinen Kopfschutz unter den Arm und lässt sich entspannt auf ein Gespräch ein. Der Mann mit dem sanften Blick steht um 2.15 Uhr auf. Seine Frau schläft dann natürlich noch. „Ich frühstücke erst einmal sauber, schließlich geht die Arbeit um vier Uhr los.“ Mittags ist Fischer wieder zu Hause. „Da hat man noch was vom Tag“, sagt der stolze MANler, der sich von Freunden immer wieder anhören muss, ob er überhaupt etwas arbeite. Die Spötter sollten ihn einmal in der Gießerei besuchen, dann, wenn er das heiße Eisen zum richtigen Moment in eine der beiden Wannen ablaufen lässt. Eine Sirene ertönt zuvor. Ein lautes Piep, Piep, Piep. Gespannte Ruhe. Eher ein wildromantischer als brachialer Moment. Der Ring der Nibelungen oder Rammstein passen nicht zu Fischer und seinen feinfühlig wirkenden Kollegen. Eher etwas Lyrisches, vielleicht Wagners Ouvertüre zum Lohengrin oder die Morgenstimmung aus Griegs Peer-Gynt-Suite.
Die Augsburger MAN-Geschichte
Die Wurzeln des Unternehmens MAN, das heute zu Volkswagen gehört, reichen zurück bis zur Inbetriebnahme der St. Antony Hütte in Oberhausen am 18. Oktober 1758.
Dass Augsburg zu einer der wichtigsten MAN-Städte werden sollte, ist letztlich dem Unternehmer Ludwig Sander zu verdanken, der 1840 dort eine Maschinenbau-Fabrik gründete, um eine lokale Weberei direkt mit Textilmaschinen zu beliefern.
Sander verpachtet die Fabrik 1844 an Carl August Reichenbach und dessen Schwager Carl Buz. Sie stellen den Bau von Textilmaschinen ein und setzen stattdessen auf Dampf- und Druckmaschinen. 1844 kommt die Schnellpresse auf den Markt, 1873 die Rotationsdruckmaschine für den Zeitungs- und Buchdruck, die Großauflagen und Massenmedien ermöglicht.
1857 wird das Werk in eine Aktiengesellschaft unter dem Namen „Maschinenfabrik Augsburg AG“ umgewandelt. Carl von Linde lässt seine Kältemaschine ab 1873 in Augsburg unter Lizenz bauen. So kann etwa Bier dauerhaft gelagert werden.
Ab 1893 entwickelt Rudolf Diesel in Augsburg den Diesel-Motor, die wichtigste Innovation für MAN.
Nur 100 Sekunden dauert das eher ruhige Finale des gelb leuchtenden, sich ergießenden Eisens. Stunden wurde darauf hingearbeitet. An dem Morgen wird ein gut elf Meter langer, 3,50 Meter breiter und 2,5 Meter hoher Motorblock gegossen. Das Bauteil ist mehr als 100.000 Euro wert. Da sollten keine Fehler passieren. Über sechs Rohre an jeder Seite des im Boden eingelassenen Beckens tritt das Eisen in die Form ein. Auch wenn Fischer und seine Kollegen viel Erfahrung haben, warnen sie sich selbst: „Das Wichtigste ist, konzentriert zu bleiben, nicht zu viel Routine aufkommen zu lassen.“
Der Motorblock bleibt in der Grube, ehe er auf 300 Grad abgekühlt ist
Am Ende hat es wieder geklappt. Die Geburt verlief erfolgreich. Die Motor-Väter lächeln. Die Anspannung fällt langsam ab. Doch kein Abklatschen, kein Siegesjubeln, keine Selbstzufriedenheit. Vier Wochen bleibt der Motorblock in der Grube, ehe er auf 300 Grad runtergekühlt ist. Dann wird das Teil ausgebaggert, vom Sand befreit und mit einem Kran rausgehoben, um sechs weitere Wochen vor sich hin zu erkalten. Erst jetzt bekommt er nach einem Feinschliff sein kompliziertes Innenleben, wird umfangreichen und teuren Tests auf Prüfständen unterzogen, schließlich soll so ein Motor Jahrzehnte verlässlich laufen.
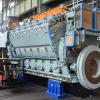
Die 240 Mitarbeiter der Gießerei bilden eine Fabrik in der Fabrik mit ihren insgesamt rund 4000 Beschäftigten. Die Eisenschmelzer halten besonders zusammen. In der Gießerei merken sie es rasch, wenn eine Branche wie zuletzt die Öl- und Gaswirtschaft wegen des Preisverfalls massive Probleme bekommt. Die Förder-Unternehmen kauften weniger Schiffe, also auch weniger Motoren aus Augsburg. Kurzarbeit war die Folge. Es läuft aber wieder besser, zumindest bei den Schiffsmotoren. Dafür verantwortlich ist auch ein Niederländer, der sechs Jahre zur See als Schifffahrts-Ingenieur gefahren ist und heute weltweit den Vertrieb der etwa in Kreuzfahrtschiffen eingesetzten MAN-Viertaktmotoren leitet. Lex Nijsen lebt mit Frau und Kindern seit fünf Jahren in Augsburg. „Uns gefällt es hier. Das Leben in Bayern ist echt nicht schlecht“, sagt er im Gespräch gleich zweimal lachend in Holländisch gefärbtem Deutsch. Auch Nijsen scheint für Augsburg echt nicht schlecht zu sein. Er spricht die Sprache der Schiffsbauer und Reeder. „Für mich ist das Glas immer halb voll“, betont der Manager, der beim Besuch des holländischen Königspaars am Abendempfang in der Münchner Residenz teilnahm. Der Optimist Nijsen spricht nicht so sehr über die weniger gewordenen Aufträge aus der Öl- und Gasindustrie, sondern über die Verkaufserfolge seines Teams bei Motoren für Kreuzfahrtschiffe und schnelle Fähren. Letztere Boote verbrauchen viel Sprit, was beim derzeit niedrigen Ölpreis für die Betreiber von Vorteil ist. So geht ein MAN-Motor für eine High-Speed-Fähre nach Australien.
In der Wirtschaftswelt steht alles mit allem in Verbindung. Lokal und global sind zwei Seiten einer Medaille. Dass Fischer und seine Kollegen trotz schwieriger Marktlage noch Motorblöcke gießen können, hängt auch mit dem Verkaufstalent eines einstigen holländischen Seemanns zusammen, der eine Lederhose besitzt, für Augsburg schwärmt und stolz darauf ist, dass MAN auch den Motor für ein in Singapur gebautes Riesenschiff mit einem Mega-Schwenkkran liefert.